RESEARCH AND INNOVATION
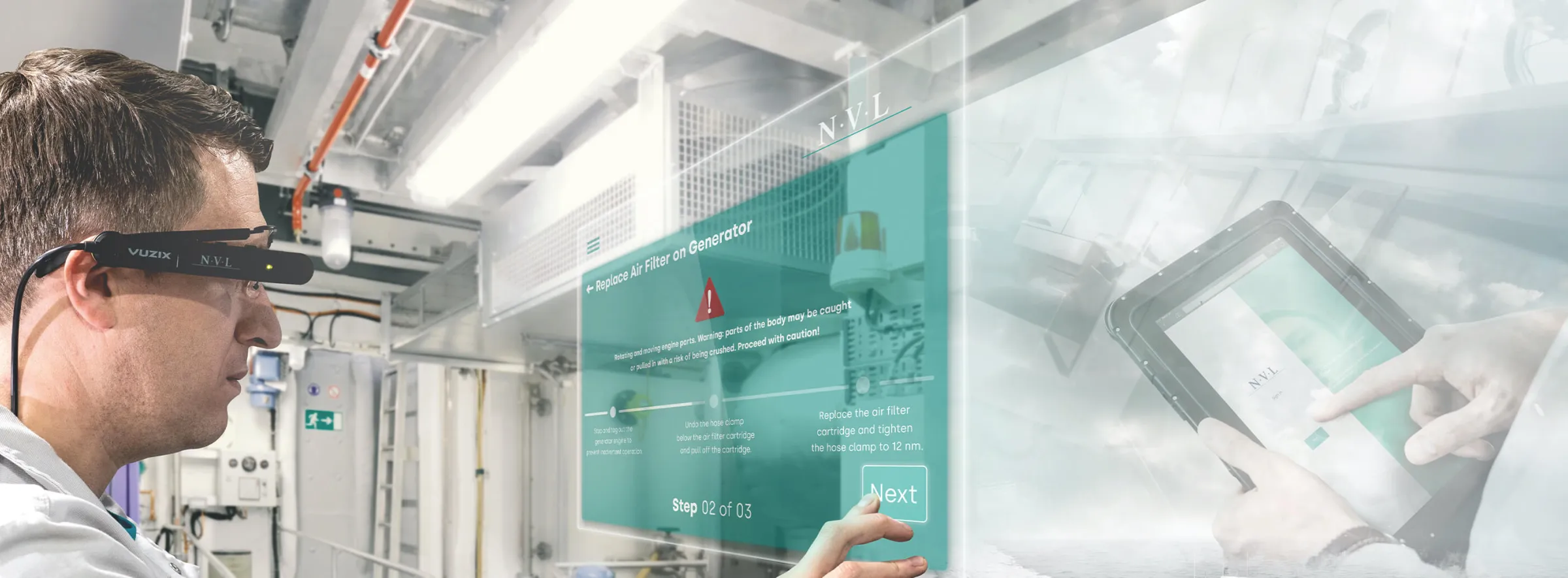
PIONEERS IN INNOVATION AND DIGITAL TRANSFORMATION
At NVL, we have a strong track record of being pioneers in many technical areas and are always looking to shape the future of the shipbuilding industry. Since our beginnings, we have created a vast pool of experience and know-how, which we continuously nurture and grow.
Technological progress is a major part of our forward-thinking approach when it comes to innovation and digitalisation (I&D). It is supported by NVL’s organisational structure and the use of lean principles, which also reflect our mindset towards innovation.
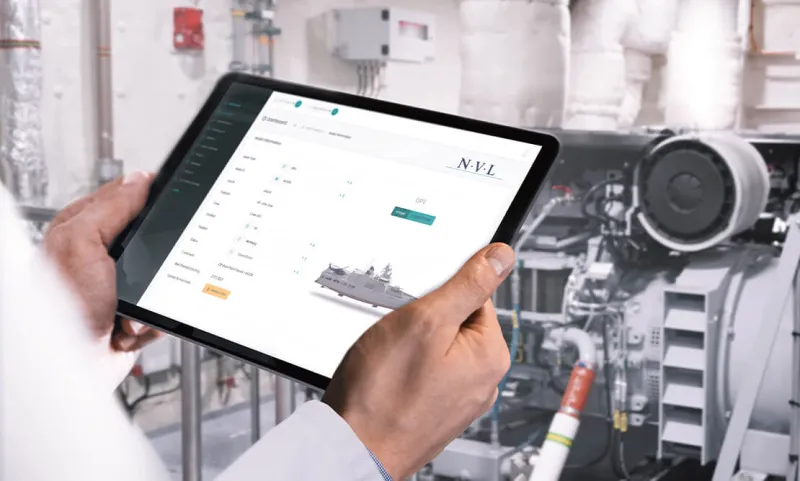
FORWARD THINKING FOR TODAY’S COMPLEXITY
To face the challenge of ever more complex vessels and technological needs, we have developed a clear organisational structure for managing innovations. We aim to:
- Develop a group-wide I&D agenda
- Identify promising new methods and technologies
- Prioritise topics for further research
- Select initial applications for analysing future potentials
- Implement the right innovations at the right time, processes and costs
Backed by our structured approach, we are able to offer you a range of product innovations and services that match your vessel and operational needs, providing you with the latest technology. We work together with our customers and partners to find the most suitable tailored solutions and to offer high quality at a competitive price.
INNOVATIONS THAT PUT THE CUSTOMER FIRST
With our on-board products, we implement innovation with the aim to improve efficiency and reliability in operation while ensuring a longer life cycle and easier maintenance and repairs of our vessels. By generating a digital twin, we provide a digital base for the operational phase, test technologies in advance and implement measures more quickly.
Innovations also serve to support us in making our value chain and processes more efficient and faster while assuring a high level of quality for the vessel – not only for our own operations but also for those of our customers.
We are continuously open to collaborations with companies and start-ups for new solutions. Please feel free to contact us for more information.
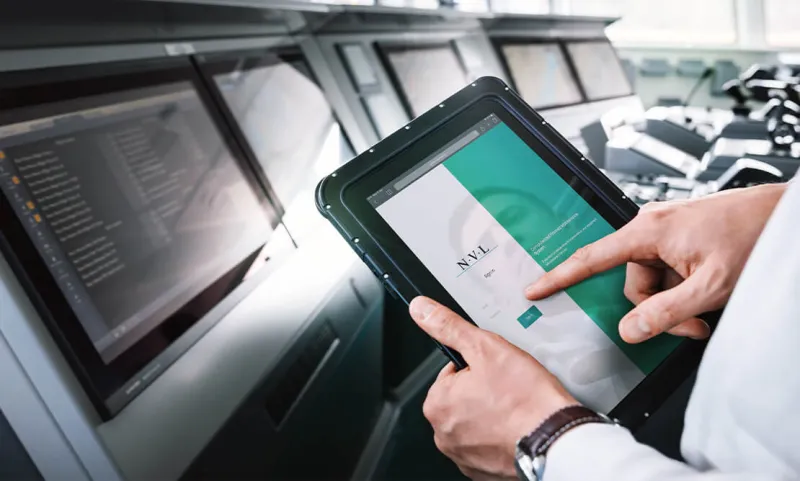
GOING DIGITAL TO GO FURTHER
In today’s complex world, digital transformation has become more essential than ever – particularly in shipbuilding. At NVL, digitalisation goes hand in hand with innovations and process improvements, making our value chain and your vessels more efficient over their entire life cycles. We face the challenges, dig behind the buzzwords and discover the value in the technologies.
Our digital transformation initiative was launched in 2018 and covers the following topics:
- Within our shipyard infrastructure, we increase the efficient use of resources and reduce risk through online monitoring and control of key resources. As one example, our YardManagerApp gives our employees 24/7 digital access to key infrastructure equipment for our shipbuilding process.
- With the development of our Naval Data Information Platform (NDIP), we cover full information management of data across all phases – from design to construction to aftersales services. With NDIP, we ensure that the right information is available at the right time and at the right spot.
- Across the shipbuilding process and along the whole value chain, we support our employees by providing apps with helpful digital tools to boost their performance, for example through paperless working in pipe production or during acceptance tests and commissioning procedures.
- For on-board operations, we design and implement systems and components for more transparency over the current status of your vessel. This supports the crew and the onshore team in executing their mission while assuring the highest possible availability.
OUR YARD MANAGER APP
In addition to regular maintenance measurement and handling features, a Neue Jadewerft dock was equipped with various sensors and network components to transfer encrypted data to an in-house cloud solution. To access these data, we developed the YardManagerApp. With this app, our employees are now able to check the current status of the dock online and from anywhere. The app shows data like tilt on the x- and y‑axis, ballast tanks status, air pressure, energy and fire-extinguishing water supply, the temperature of the heating system, and the latest weather data. In case of an emergency or if any data seem critical, an alarm informs the user to check the dock. The app reduces the amount of time for inspection rounds, minimises risks of severe damage and outages, and optimises maintenance.
The concepts and data structure of this app are today being universally used and easily adapted to critical infrastructure in all our shipyards, for example to monitor compressors, transformers and humidity conditions during paint application or to control an extended energy monitoring system.
OUR RESEARCH PROJECTS
At NVL, our goal is to always find the best solution for our customers. In order to meet the needs of tomorrow, we continuously invest in research, development and innovation. The research topics vary from process optimisation to new product development. A large number of projects are being processed internally and in parallel to our shipbuilding work. Other topics are handled within the framework of funded joint projects, where we cooperate with excellent partners from academic, scientific and business sectors.
We are always interested in new collaborations and ideas. Please contact us for more information.
Sea Defence
Survivability, electrification, automation, detectability, enabling foresight of European naval capabilities in extreme conditions
The goal of this research project is to prepare a road map of technologies to be included in the next generation of naval platforms and pursued in further European development programmes.
Duration: 1 December 2020 – 31 May 2023
Project partners:
- DAMEN SHIPYARDS GROUP, Netherlands
- FINCANTIERI S.P.A., Italy
- NAVAL GROUP SA, France
- NAVANTIA, S.A., S.M.E., Spain
- SAAB KOCKUMS AB, Sweden
- SEA EUROPE, Belgium
- THYSSENKRUPP MARINE SYSTEMS, Germany
- ODENSE MARITIME TECHNOLOGY, Denmark
- NVL B.V. & Co. KG, Germany
- TNO, Netherlands
- MARIN, Netherlands
- CTN, Spain
IntRobAS
Intelligent robot systems for component manufacturing in shipbuilding
In addition to digitalisation, automation is an important tool for boosting productivity and competitiveness. IntRobAS is a research project for the development of an intelligent robot system for welding micro-panels and volume structures without needing 3D data from construction. An important goal is the development of an artificial intelligence (AI) tool for drawing up an automatic welding programme. The aim is also to build a suitable system which enables very flexible component manufacturing and the largely automatic high-quality welding of components through the help of cutting-edge sensors and safety technology as well as a special human–machine cooperation that is a novelty in shipbuilding.
Duration: 1 February 2020 – 31 January 2023
Based on the latest manufacturing process and the planned human–machine cooperation, the requirements for system, operational and safety concepts of a robot-supported, sensor-based manufacturing process were defined and provided to the project partners as a basis for the system concept. For the development of the AI tool, construction standards, mock-up structures and requirements for special forms of welding and welding results were determined.
Project partners:
- Peene-Werft GmbH & Co. KG
- IMG – Ingenieurtechnik und Maschinenbau GmbH
- Fraunhofer-Institut für Großstrukturen in der Produktionstechnik IGP
ProNoVi
Analysis methods and design measures for the reduction of noise and vibration induced by marine propellers
The main goal of ProNoVi is the improvement of the numerical and experimental methods for forecasting noise and vibrations caused by the configurations of propellers and ship hulls. Furthermore, practical recommendations for reducing the noise and the vibration levels should be developed for specific use cases.
Duration: 1 June 2018 – 30 November 2021
Numerical methods have been improved, for example in regard to the forecasting of cavitation, as the basis of noise and vibration calculations. This was supported by model trials in the partners’ testing facilities. The trials were performed with the improved numerical methods, thus enabling the verification of numerous parameters. As a result, there were a few adjustments needed which are currently in the final implementation phase. But even in the prototype phase, the tools were already able to be used in terms of practical recommendations for ship designs.
Project partners:
- Fr. Lürssen Werft GmbH & Co. KG, Germany
- Schottel GmbH, Germany
- TUHH Institute for Fluid Dynamics and Ship Theory, Germany
- SINTEF Ocean, Norway
- CNR Insean, Italy
- Helseth AS, Norway
KeSS
Compact and efficient emissions after-treatment to minimise nitrogen oxides and noise emissions
The reduction of acceptable NOx emission requires additional after-treatment. An approved technical solution is the use of an SRC catalyser. However, this takes up a significant amount of space. With KeSS, we developed an idea of a combined emissions system with silencers and an SCR catalyser in just one shell. This system would be 30% smaller, lighter and more affordable than conventional systems comprising single components.
Duration: 1 April 2015 – 30 June 2017
Prototype of the 4 MW test system
Comparison between a conventional emissions after-treatment system and the new, innovative KeSS system
The idea was realised and successfully tested for a 4 MW system. Afterwards, different variants were tested on a 500 kW engine. This resulted in the definition of two generally suitable concepts which could be used respectively depending on the construction conditions. The space, weight and cost savings aimed for were achieved. Today, two ships which feature the certified KeSS system have been successfully delivered. The partners have applied for a patent for the KeSS system.
Project partners:
- Fr. Lürssen Werft GmbH & Co. KG
- HUG Engineering GmbH
- Nießing Anlagenbau GmbH
About NVL
We invite you to learn more about who we are and what we stand for at NVL. If you have any questions, please don't hesitate to contact us.